
La función de la Turbina es convertir parte de la energía que tienen los gases que salen de la cámara de combustión y la atraviesan (expansionándose en ella como se indicó en el ciclo termodinámico) en trabajo mecánico (al hacer girar la parte rotatoria de la turbina) y que se emplea, a través del eje que los une, en mover el compresor al que está unida y, a través de otro eje transversal que engrana con el eje principal, en mover la caja de accesorios y los accesorios (tanto del propio motor como de servicio al avión) que se encuentran conectados a ella. En un turborreactor básico la turbina emplea en ese cometido aproximadamente un tercio de la energía total que se genera en el proceso de combustión en la cámara.
La energía restante es la que posteriormente se transformará en empuje de propulsión en la tobera del motor.
Generalmente en los motores turbohélices y turboejes, cuando la hélice o el eje de salida de potencia no están conectados directamente a la turbina única, hay una segunda turbina que trata de extraer la mayor parte de la energía que tengan los gases después de haber pasado por la turbina que mueve al compresor y, a través de un eje independiente, transmiten la transmiten en forma de trabajo mecánico a la hélice (propulsor) o al eje de potencia (en el caso de los turboejes). Módulo
Hay que señalar que cuando el conjunto compresor‐turbina se mueve de forma estacionaria se cumplen las condiciones siguientes:
• El gasto de aire a la salida del compresor es igual al gasto de gases que atraviesa la sección de turbina más el posible gasto de aire que se haya podido “sangrar” en el Difusor pre‐cámara(s).
• Las revoluciones con que giran compresor y turbina solidaria son las mismas.
• El trabajo mecánico cedido por la turbina es igual al que absorben el compresor y el conjunto caja de accesorios‐accesorios movidos por ella (si excluimos las pérdidas mínimas por rozamiento que pueda haber en los ejes de transmisión entre turbina y compresor y entre eje principal y caja de accesorios).
• La diferencia entre las presiones a la entrada de la turbina y la salida del compresor es igual a las pérdidas de presión habidas en el difusor y en la(s) cámara(s) de combustión.
Hay dos tipos de Turbinas (correspondiendo con lo que ocurre en el caso de los compresores): Centrípetas y Axiales. La Turbina Centrípeta tiene una configuración similar al Compresor Centrífugo, pero el sentido de movimiento del flujo de gas que la atraviesa es inverso (colector – difusor – impulsor). Se utilizan solo para pequeños motores como la Unidad de Potencia Auxiliar (APU) y en equipos accesorios del avión, pero no en motores de reacción.
Turbina axial:
El flujo de gases en la turbina axial se mueve, como su nombre indica, paralelamente al eje del motor. Está constituida por sucesivos escalones (o etapas) formados cada uno de ellos por un estator y un rotor (en este orden en el sentido de avance del flujo de gases). Cada “anillo” o “corona” de estator está formado por una cascada de álabes (“vanes”) geométricamente dispuestos de la misma forma radial que los del rotor, pero que se encuentran fijos a la carcasa exterior o cárter de turbina.
Cada “rueda” de rotor de un escalón de turbina axial está constituida por una cascada de álabes (“blades”) en sentido radial, espaciados regularmente y dispuestos circunferencialmente encastrados sobre un disco. Todos los discos de los escalones del rotor están unidos solidariamente al eje que mueve al compresor cuando la expansión de los gases al pasar por la turbina le hace girar (al rotor).
En los motores turborreactores con más de un compresor y en motores turbofan con uno o dos compresores y un fan, cada uno de ellos está unido a una turbina independiente mediante un eje.
Todos los ejes son coaxiales y también independientes. En el caso, por ejemplo, de haber dos compresores la primera turbina o turbina de “alta presión” (HPT) mueve al compresor de “alta presión” (HPC) y la siguiente o turbina de “baja presión” (LPT) mueve al compresor de “baja presión” (LPC).
Como vimos para los compresores axiales la sección de paso va disminuyendo a medida que el aire lo atraviesa, ya que se va comprimiendo. En el caso de la turbina ocurre lo contrario, la sección de paso va aumentando, porque el gas se va expansionando (ocupando mayor volumen específico). Es menor el número de escalones de turbina necesarios que el que era preciso para el compresor axial (1 escalón de turbina por hasta 5, o incluso más, escalones del compresor al que arrastra).
Es debido a que el trabajo mecánico específico que se puede extraer de cada escalón de turbina es muy superior al que cada escalón de compresor puede suministrar al aire que comprime y eso es así porque, aunque sean iguales la velocidad de rotación de compresor y turbina y la velocidad axial de paso del fluido por ambos, la deflexión de la corriente de gas que se puede conseguir en la turbina es mucho mayor que la que el compresor puede imprimir al aire que lo atraviesa. Se define el “grado de reacción” de un escalón de turbina como la relación entre la expansión (variación de energía) que sufre el gas en el rotor en relación con la expansión total en todo el escalón.
El grado de reacción deseado para una turbina se consigue mediante la selección adecuada de los perfiles de los álabes de rotor y estator. Las turbinas de grado de reacción cero se denominan “Turbinas de Acción o Impulso”, es decir, aquellas en que toda la expansión del gas tiene lugar en el estator, para lo que la sección de paso entre sus álabes tiene forma de tobera convergente (es mayor a la entrada que a la salida) y el gas a su paso por ellos se acelera (hasta casi la velocidad del sonido) y disminuye su presión y temperatura. A la salida del estator la corriente de gas es deflectada en el sentido de giro del rotor a fin de que impacte con un ángulo de ataque apropiado con los álabes del rotor cuando este está girando.
Los álabes del rotor de la “Turbina de Acción” tienen una sección de paso constante entre ellos. El gas a su paso no sufre variaciones de presión, temperatura o velocidad relativa (respecto a los álabes). El par de giro en el rotor es producido por la fuerte deflexión que la corriente de gas a gran velocidad sufre al pasar por el.
Las turbinas cuyo grado de reacción es distinto de cero se denominan genéricamente “Turbinas de reacción”. En ellas la expansión del gas tiene lugar tanto en el rotor como el estator (en mayor o menor medida en cada uno según el grado). Tanto los álabes de estator como los del rotor forman secciones de paso en forma de tobera convergente en que el gas se acelera, se enfría y sufre una caída de presión. La deflexión de la corriente del gas y su aceleración en los canales de paso entre álabes del rotor es la causante de crear una fuerza de reacción (efectiva) en el rotor que produce el (par de) giro de la turbina. “Turbina de reacción pura” es la que tiene un grado de reacción igual a uno.
Es decir, toda la expansión del gas se produce en el rotor y los álabes del estator lo único que hacen es deflectar y dirigir la corriente de gas en el sentido apropiado hacia el rotor. En realidad la mayoría de las turbinas de los motores actuales no tienen un grado de reacción único, sino que este va variando de la raíz al extremo de los álabes. Es decir, la forma de los perfiles y sus secciones de paso van variando a lo largo del álabe.
En la raíz el perfil de los álabes es más de “acción” (grado de reacción menor) y el “grado de reacción” crece gradualmente hacia el extremo del álabe. Este tipo de Turbinas se llaman de “Acción – Reacción”. A la salida de la sección de combustión el flujo de gas tiene prácticamente una distribución uniforme de presión, temperatura y velocidad, pero al salir del primer estator de turbina ya hemos visto que ha sido deflectado fuertemente.
La(s) turbina(s) se diseña(n) para que a la salida del último rotor el flujo de gas haya recuperado un movimiento axial uniforme antes de entrar en la tobera, ya que de lo contrario perdería eficiencia la expansión en ella y se producirían indeseables vibraciones y posibles daños estructurales en esa zona del motor.
La uniformidad en la velocidad axial del flujo a la salida del (último) rotor se logra dando una cierta torsión (“retorciendo”) a los álabes tanto del estator como del rotor (el ángulo de torsión de estos últimos es mayor en el extremo del álabe que en la raíz) con lo que el trabajo extraído del flujo uniforme de gas procedente de la combustión es igual en cualquier posición a lo largo del álabe.
Esto provoca que haya variaciones de velocidad y presión (también de temperatura) a lo largo de los álabes entre la entrada y la salida de la turbina como esquemáticamente se muestra en las Figuras siguientes
La mayor presión en el extremo del álabe del rotor (a la entrada en el) reduce las pérdidas que se producirían hacia afuera por fuerza centrífuga, mejorando así el rendimiento del álabe. También se reducen las pérdidas de presión por el extremo del álabe del rotor mediante álabes que tienen un especie de “sombrerete” o “placa de apoyo” en el extremo (“shroud”). Las placas de apoyo de todos los álabes (“apoyados”) engarzan entre si formando una especie de anillo que los rodea y evita además en gran medida la vibración de los extremos de los álabes (presente en los álabes “en voladizo”), aunque no se utilizan si se trata de álabes funcionando en situación muy crítica ya que la placa de apoyo aumenta considerablemente los esfuerzos por fuerza centrífuga a que está sometida la raíz del álabe.
Los álabes de turbina están sometidos a los mismos esfuerzos (flexión, tracción y esfuerzos secundarios debidos a desalineación de los centros de gravedad de los perfiles del álabe) que los álabes de compresor.
Pero además los álabes de turbina (tanto de estator como de rotor) están sometidos a los esfuerzos originados por las altas temperaturas a las que operan (esfuerzos de “termofluencia”) y que originan fallos específicos de estos elementos por: • Fluencia del material (deformación progresiva debida a la carga aerodinámica). • Fatiga térmica (motivada por las fuertes variaciones de temperatura a que están sometidos que da origen a la aparición de grietas).
• Corrosión y oxidación.
• Agravamiento de los esfuerzos debidos a fuerzas centrífugas y vibraciones. La zona más crítica de los álabes del rotor de turbina es su encastre con el disco (que suele tener la forma de “copa de abeto”), pero si se trata de álabes “apoyados” además la punta extrema del álabe.
Las técnicas desarrolladas para paliar los efectos de la alta temperatura de operación de los elementos de turbina se basan en su refrigeración (automática) mediante aire “sangrado” del propio motor (desde etapas intermedias del compresor hasta del flujo secundario de cámara(s) de combustión). El aire sangrado se canaliza por pasajes en el interior del motor hasta el interior de los álabes (tanto de estator como de rotor), que están dotados de huecos internos a fin de dejar pasar este aire de refrigeración y que es devuelto a la corriente de gas de la turbina a través de orificios de salida. Los métodos de refrigeración empleados son:
• Convección.
• Convección forzada.
• Película refrigerante.
• En fase aún de desarrollo está la refrigeración por Transpiración (álabes porosos). Los materiales empleados en el diseño y la fabricación de turbina deben responder a las condiciones en que operan (la zona más crítica de todo el motor):
• Alabes de estator: Materiales resistentes a altas temperaturas, a la oxidación‐corrosión y al choque térmico. Son alecciones de moldeo de base níquel o cobalto y protección cerámica
• Alabes de rotor: Materiales que soporten la combinación de temperatura‐carga más alta de todo el motor y que por tanto no sean afectados por los fenómenos de termofluencia.
Se usan superaleaciones de base Níquel‐Cromo con Cobalto, hierro y diversos aditivos más (“Nimonic”).
Además de la refrigeración de álabes ya descrita el empleo de otras técnicas metalúrgicas de fabricación de álabes de rotor han posibilitado una mejora sustancial de comportamiento ante las exigentes condiciones de funcionamiento, y estás técnicas son la “solidificación direccional” y los álabes “monocristal”.
• Discos de turbina: Tienen que soportar diferencias de temperatura de hasta 300ºC entre el centro y la periferia. Se utilizan desde aceros inoxidables (austeníticos) con adición de molibdeno o niobio que tienen buen comportamiento a muy altas temperaturas, hasta superaleaciones de hierro‐ cromo‐níquel que resisten elevados esfuerzos a alta temperatura. Otras aleaciones también usadas son de níquel‐cromo‐cobalto con adición de aluminio y titanio (eje.: “Waspaloy”).
• Cárter de turbina: Se emplean aceros inoxidables resistentes a altas temperaturas.



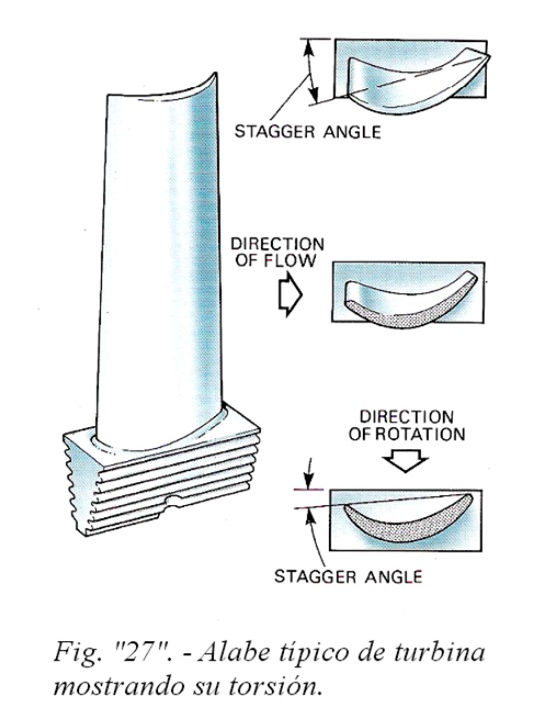
